Introduction
PVC (polyvinyl chloride) piping is a popular, versatile option for both interior and exterior plumbing and drainage applications. Its flexibility, durability, and affordability make it an ideal choice for projects ranging from irrigation systems to drain, waste, and vent lines.
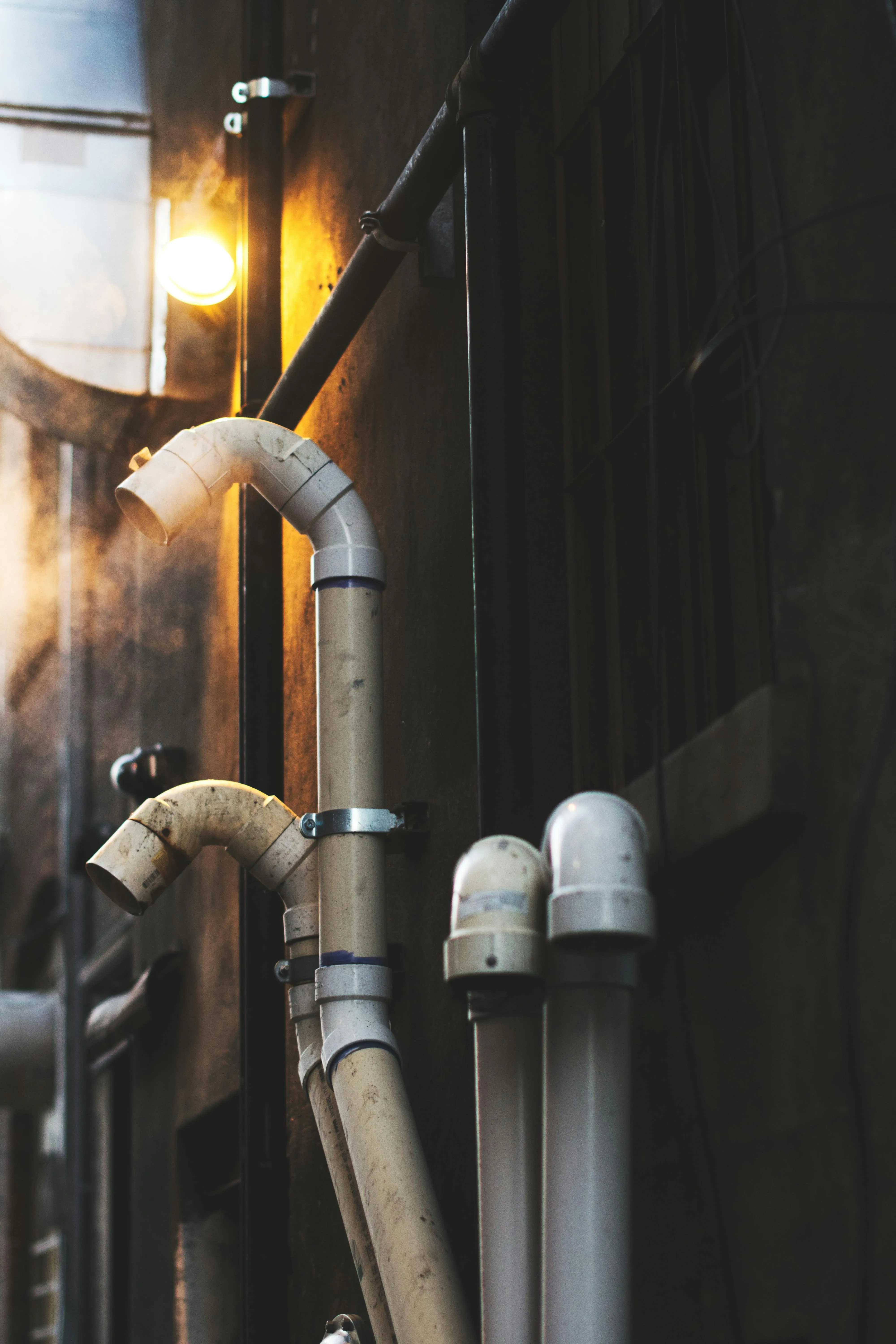
Compared to traditional metal pipes, PVC offers many benefits. It is corrosion resistant, meaning it won't rust or degrade over time. PVC is also lightweight yet strong, and it provides smooth water flow thanks to its inside diameter consistency. Furthermore, PVC pipe is easy to install, modify, and repair using simple tools.
When working with PVC pipe, you'll need to measure, cut, deburr, prime, cement, and connect the pipes and fittings. Proper preparation is key to creating watertight joints that will hold up for decades. With some basic knowledge and the right techniques, connecting PVC pipe is a straightforward DIY project for running new plumbing in a home or building.
The main steps include:
- Gathering the necessary PVC pipe, fittings, primer, cement, and tools
- Measuring and cutting the pipes to the required lengths
- Deburring the ends of the cut pipe to ensure proper adhesion
- Applying primer to prepare the surfaces
- Applying cement to bond the joints
- Connecting the pipes and fittings while the cement is still wet
- Allowing adequate time for the cement to fully cure before pressurizing the system
- Insulating pipes as necessary to prevent condensation buildup
- Testing the system once fully assembled to check for leaks
Gather the Necessary Materials
Before you begin, make sure you have all of the necessary materials on hand for connecting PVC piping. The key materials you'll need include:
- PVC pipes - These are the straight sections of pipe that you'll cut to length and join together with fittings. PVC pipe is sold in 10 or 20 foot lengths and in different diameters depending on your project. Measure your project to determine what diameter and lengths you'll need.
- PVC fittings - Fittings allow you to connect pipes together and route them in different directions. Common PVC fittings include elbows, tees, reducers, caps, and more. Take measurements and sketch out your piping layout to determine which fittings are required.
- PVC primer and cement - PVC connections are assembled using a two-step process with primer and cement. The primer prepares and softens the surfaces, while the cement chemically fuses the pieces together. Use products designed for PVC and follow the manufacturer's instructions.
- Pipe cutter - A pipe cutter is a specialized tool for cutting PVC pipes cleanly and squarely to the proper length. Ratcheting plastic pipe cutters that fit over the pipe exterior are quick and easy to use.
- Deburring tool - After cutting, use a deburring tool to remove any plastic burrs or ridges from the inside and outside of the pipe ends. This ensures proper sealing with fittings. Look for a PVC deburring tool or reamer.
Once you have these essential supplies, you'll be ready to start connecting pipes. It's a good idea to lay out all the pieces and do any necessary measurements or pre-assembly before cementing anything together.
Measure and Cut the Pipes
Measuring and cutting PVC pipes properly is crucial for a leak-free plumbing system. Here are some tips:
- Measure twice and cut once. Take precise measurements and mark the pipe. It's easy to cut off more, but impossible to add length back.
- Allow an extra 1/4 inch on each end for fittings. The pipe should slide fully into fittings.
- Use a mitre box guide when cutting to ensure straight cuts at the desired angle. Mark the pipe at the edge of the box.
- For straight cuts, use a PVC ratcheting cutter. Place the pipe in the cutter so the blade aligns with the mark. Ratchet the cutter handle to slice through the pipe.
- Make gentle curves and bends by cutting a series of short shallow V notches on the concave side.
- For tight bends, use a PVC pipe and tubing bender. Mark the bend, heat the pipe, and bend it slowly.
- When using any cutting tool, firmly secure the pipe to prevent slipping. Wear gloves to protect hands.
- Ensure nobody is in the path of the blade when cutting. Stand to the side, not behind the pipe.
- Let cut pieces of pipe fall to the ground rather than trying to catch them. Sharp edges can cause gashes.
Accurate measuring and straight cuts will allow the pipes to fit together correctly for a secure, leak-free system. Take it slow and double check all measurements.
Deburr the Pipes
Properly deburring PVC pipes is an important step when connecting pipes. Any rough edges or burrs left on the pipes can prevent proper sealing and lead to leaks down the road.
To deburr PVC pipes:
- Use a knife or plastic deburring tool to remove any burrs or ridges from the inside and outside of the pipe ends after cutting. Be careful not to scratch or gouge the pipe.
- Run a clean dry cloth over the cut ends to remove any plastic debris.
- For larger pipes, a reamer or deburring blade can be used to cleanly chamfer the edges. Spin the blade around the interior and exterior of the pipe end.
- Visually inspect the pipe ends and feel with your fingers to ensure all burrs are removed. There should be no sharp edges.
- Remove all plastic shavings from the pipe interior so they don't end up in the piping system.
Proper deburring creates smooth, beveled edges that allow for even cement application and prevent the pipe from getting scratched during assembly. Taking the time to deburr PVC pipes helps ensure a strong, leak-free connection.
Apply Primer
Primer is a vital component for creating watertight PVC pipe connections. It serves several key purposes:
- Softens and prepares the surfaces of the PVC pipe and fittings for cement application. The primer contains solvents that slightly melt the surfaces of the PVC, allowing the cement to bond more effectively.
- Removes dirt, grease, and moisture from the PVC surfaces. Any contaminants left on the pipe or fittings can prevent the cement from properly fusing to the PVC.
- Provides a "dry" surface for the cement to adhere to. The solvents in the primer evaporate quickly after application, leaving the PVC ready for cementing.
To properly apply primer:
- Wear protective gloves, as primer contains harsh solvents that can irritate skin and eyes. Work in a well-ventilated area.
- Use a dauber applicator, small brush, or roll-on bottle. Pour some primer into a container to dip the dauber or brush into.
- Liberally apply primer into the fitting socket and onto the end of the pipe to the depth of the socket.
- Spread the primer around to thoroughly coat the surfaces, using a scrubbing motion. Apply a second coat and ensure no bare spots remain.
- Allow the primer to dry completely until it no longer feels tacky. This takes about 2 minutes. Properly primed surfaces should be dull and dry.
- Apply cement immediately while the surfaces are still activated. If the primer dries for too long before cementing, reapply fresh primer.
Proper priming is crucial for strong, leak-free PVC joints. Take care to completely coat all bonding surfaces before cementing.
Apply Cement
Cement is a crucial component for creating strong, leak-free PVC pipe connections. It acts as an adhesive to bond the pipes and fittings together.
When applying cement, it's important to follow the manufacturer's instructions closely. Here are some key steps:
- Wear gloves, eye protection and work in a well-ventilated area. PVC cement contains solvents that can irritate skin and eyes.
- Stir or shake the cement before applying to mix the ingredients thoroughly.
- Apply a thin, even layer of cement to the end of the pipe using a natural bristle brush. Avoid puddling the cement.
- Apply a thin layer of cement into the fitting socket, coating the inner surface.
- Quickly insert the pipe into the fitting socket and give it a quarter turn to spread the cement evenly.
- Hold in position for 30 seconds to prevent pipe from pushing out.
- Wipe away excess cement on the outside of the joint with a rag.
- Allow adequate cure time before pressurizing system, per manufacturer's guidelines. Cure times vary based on pipe size, temperature and humidity.
Properly applying PVC cement creates a chemical bond between pipe and fitting to seal joints. It ensures a durable, leak-free connection that will last the lifetime of the plumbing system.
Connect the Pipes and Fittings
Properly joining PVC pipes and fittings is crucial to creating a solid, leak-free plumbing system. Follow these key steps when connecting pipes:
- Ensure all pipe ends are deburred, primed, and have cement applied. Only join surfaces with wet cement.
- Align the pipe and fitting correctly, pushing together with a slight twisting motion to evenly distribute the cement.
- Hold in position 3-5 seconds to prevent pipe push-out - this allows the cement to set.
- Wipe away excess cement on the outside of the joint with a rag. A properly joined connection will show a bead of cement around the entire joint.
- Handle newly assembled joints carefully while cement cures. Avoid bending or rotating joints for at least 15 minutes after assembly.
- Support pipes with hangers, clamps, or straps to prevent stress on joints while curing. Follow spacing guidelines between supports.
- Set joints so they are fully seated and aligned. Off-center joints can leak and fail.
- Ensure joints are not under tension or compression. Allow some play for expansion and contraction.
Proper PVC pipe joining relies on correct preparation and assembly. Rushed joints that lack full cement coverage can easily fail. Take care when making connections to maximize strength and prevent leaks.
Allow Time to Cure
After gluing the PVC pipes and fittings together, it is crucial to allow adequate cure time before pressurizing the system. This gives the cement time to fully bond and seal the joints.
The cure time can vary substantially depending on the pipe size, temperature, humidity, pipe material, and brand of cement used. Always refer to the product directions for the recommended cure time. In general, a good rule of thumb is at least 24 hours of cure time at temperatures above 60°F.
For colder temperatures below 60°F, a longer cure time is needed - sometimes 48-72 hours. Temperatures below 40°F are not suitable for PVC cement curing. The joints may seem solidified in just a few hours, but the full chemical bond requires more time to properly strengthen.
Once the recommended cure time has passed, test the system by slowly pressurizing it and checking for leaks. Spray joints with water and look for bubbles, which indicate escaping air. Or you can pressurize the system and leave it for several hours, then check if pressure loss has occurred. Fix any leaks before fully pressurizing.
Allowing adequate cure time is a crucial step for durable PVC piping systems. Being impatient can lead to leaks, fractures, and other problems down the road. Follow the cure time directions and test methodically.
Insulate Pipes
Insulating PVC pipes is an important step that provides several benefits. Properly insulating pipes helps maintain water temperature, prevents condensation buildup, increases energy efficiency, and reduces noise. There are a few main types of insulation to consider for PVC pipes:
Benefits of Insulation
- Maintains water temperature - Insulation prevents heat loss from hot water pipes and heat gain on cold water pipes. This allows water to stay hot or cold longer as it flows through the system.
- Prevents condensation - Insulation wraps around cold water pipes to keep them from sweating, which causes mold, mildew and corrosion.
- Increases energy efficiency - Insulated pipes prevent heat transfer, saving energy and money on water heating costs.
- Reduces noise - Piping can make knocking and hammering noises as water flows through. Insulation dampens vibrations to keep pipes quiet.
Types of Insulation
- Tubular foam sleeves - Foam pipe insulation like Armaflex is a popular option. It's easy to cut and slide over pipes before sealing the seam.
- Fiberglass wraps - Fiberglass insulation with a vinyl or foil exterior can wrap around pipes. It may require adhesive or tape to secure in place.
- Rubber foam sheets - Flexible elastomeric foam sheets can wrap around pipes and be sealed with tape or adhesive. This insulation has a smooth exterior.
- Rigid foam boards - Polystyrene or polyisocyanurate rigid foam boards are used to insulate large diameter pipes. The boards are cut, wrapped around the pipe, and sealed with adhesive.
How to Insulate Pipes
- Clean piping so insulation adheres properly.
- Measure the circumference of the pipe and cut insulation to size allowing for a 1-2 inch overlap.
- For tubular insulation, peel back the adhesive liner, wrap it around the pipe, press the seam together firmly and re-seal the liner.
- For sheet style insulation, wrap it around the pipe overlapping at the seam, and tape or glue the seam.
- Use the appropriate insulation thickness for the pipe size and application.
- Seal all joints and seams thoroughly to prevent gaps. Air gaps will reduce the insulation's effectiveness.
- For exposed pipes, finish insulation with a weatherproof protective coating.
Properly insulating PVC pipes helps optimize efficiency and prevent problems. Follow insulation guidelines based on pipe size and type to gain the full benefits.
Test the Piping System
Properly testing the PVC piping system is a crucial final step before using the system. Performing a pressure test allows you to identify and fix any leaks or issues with the connections before putting the piping into service.
Why Pressure Test?
Pressure testing serves multiple important purposes:
- It verifies the integrity of the joints and connections. Even small leaks that may not be visible can be detected under pressure.
- It validates that the system can withstand the required pressure for its intended use.
- It provides peace of mind that the system was installed correctly and has no issues before relying on it for water, air, etc.
Performing a Pressure Test
These are the steps to pressure test PVC piping:
- Make sure all joints have fully cured first. Cement drying times vary by temperature.
- Isolate the section to be tested by closing any shut-off valves.
- Connect an air compressor or water pump to test up to the target pressure.
- Pressurize the system to 60-70 PSI. Don't exceed 100 PSI.
- Monitor the pressure gauge for at least 15 minutes. A drop in pressure indicates a leak.
- Inspect joints thoroughly. Listen and look for any signs of water or air escaping.
- Release pressure completely after testing.
Fixing Leaks
If leaks are found:
- Release all pressure fully before attempting repairs.
- Disconnect leaking joints and clean thoroughly with primer/cement.
- Re-apply cement fully and re-connect. Allow time to cure properly.
- Retest section until no leaks are found before using system.
Following the pressure testing steps helps validate your PVC piping connections and troubleshoot issues, giving you confidence in the system.
For more DIY tips and tricks, DIYwithHelp has got you covered…
If you need some professional guidance for your project, be sure to sign up for a free account with DIYwithHelp.com. Once you have an account, you can search our site (or fill out a project request form) and connect with expert tradespeople who are willing to lend their advice over scheduled video-calls.